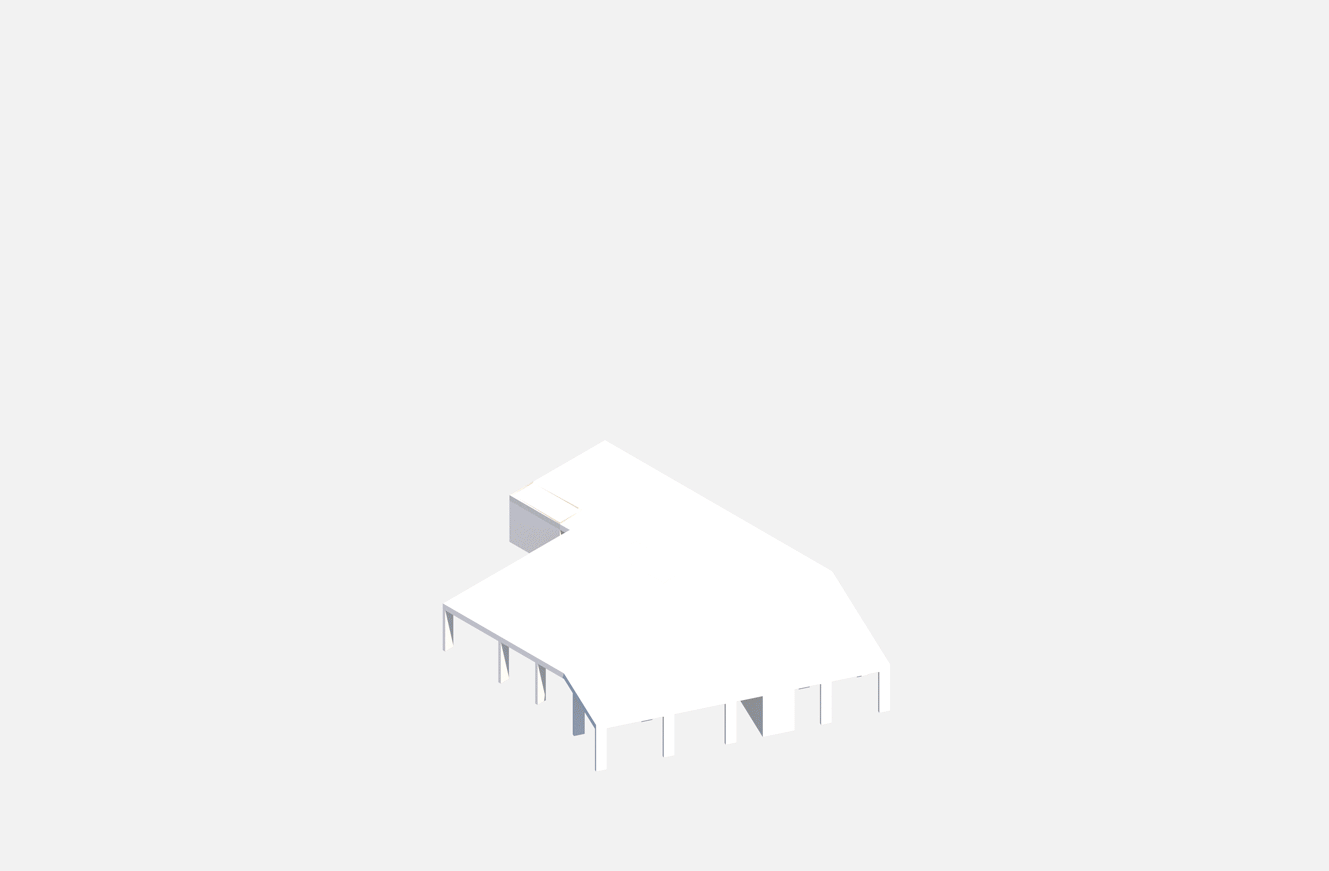
Mass timber midrise
Wayne McMillan describes how to harness design innovations in timber to create healthy, high-performance, green buildings.
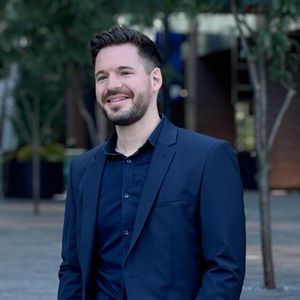
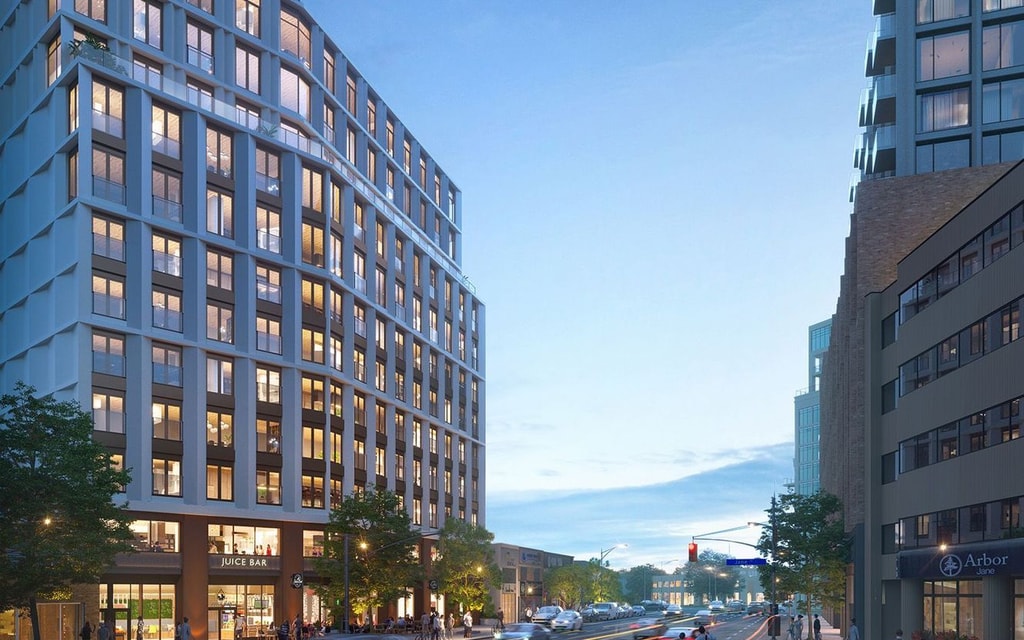
Our ever-evolving world presents both new challenges and exciting opportunities. As designers, we recognise that the way we work and live must evolve to better suit our current and future needs. By applying innovations within our practice, we can develop novel solutions that challenge the status quo and address pressing issues.
As a leading consultancy, we are harnessing ideas and expertise from our practice to create better places. By capitalising on the knowledge available from our people, we aim to identify new areas of innovation to maximise benefits for our clients, and the communities that we serve.
For example, here in Canada, the Toronto Green Standards now impose stricter performance criteria, urging the development community to re-evaluate conventional methods and materials, examine their environmental impacts, and explore alternatives.
As such, we are exploring the use of Encapsulated Mass Timber – a compelling option to design more sustainable buildings, particularly within the residential sector.
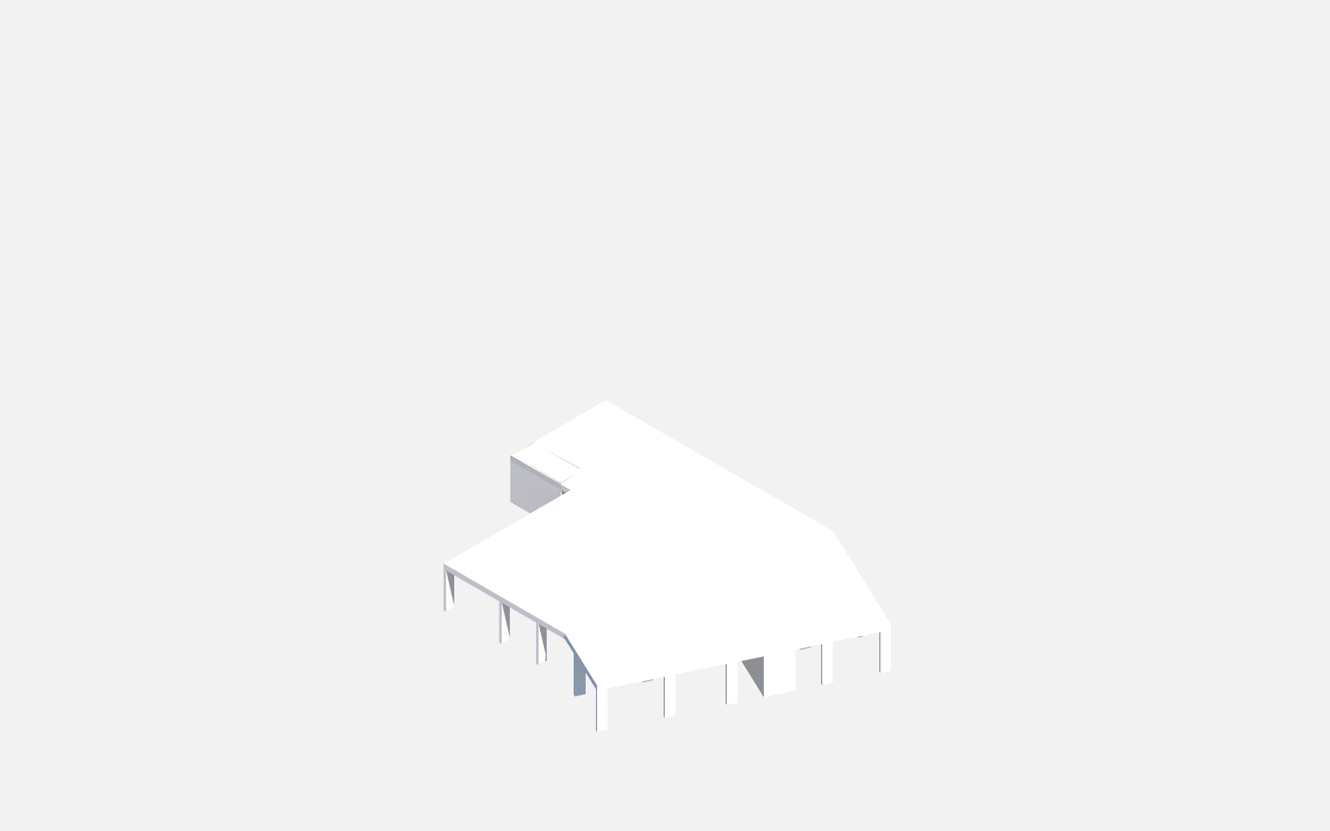
Encapsulated Mass Timber Construction (EMTC) requires an “Encapsulation Rating”, meaning timber surfaces are generally enclosed with two layers of fire-rated gypsum board. Although the timber may remain exposed within limits defined by the Ontario Building Code, encapsulation serves as a supplementary measure, enhancing the inherent fire-resistive qualities of mass timber and providing an additional layer of protection.
Under the current code, residential structures are permitted to employ encapsulated mass timber for buildings up to 12 storeys and with a floorplate area of 6,000 sq m, and recently, the Province of Ontario announced a desire to increase this height to 18 storeys. These parameters establish a practical framework, encouraging developers to consider integrating mass timber on all future midrise residential projects across Ontario.
And Toronto is a city on the rise. Specifically, the 2023 Land Needs Assessment for the City projects the potential for adding approximately 183,000 midrise units along the Avenues and in various key areas such as Downtown, Midtown, Centres, and other promising locations.
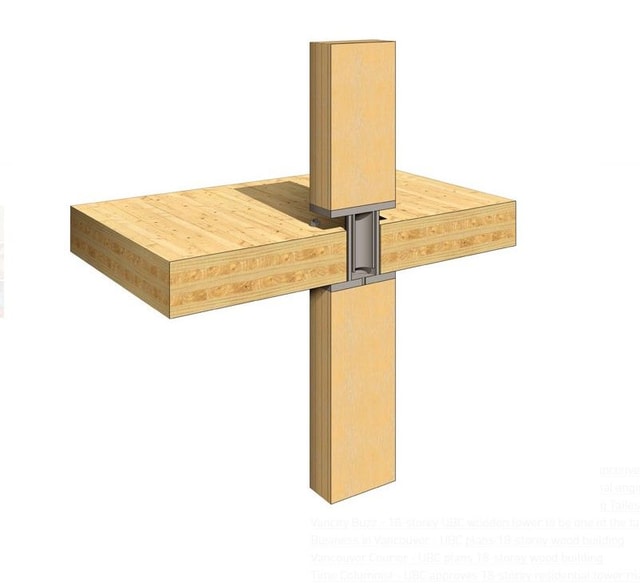
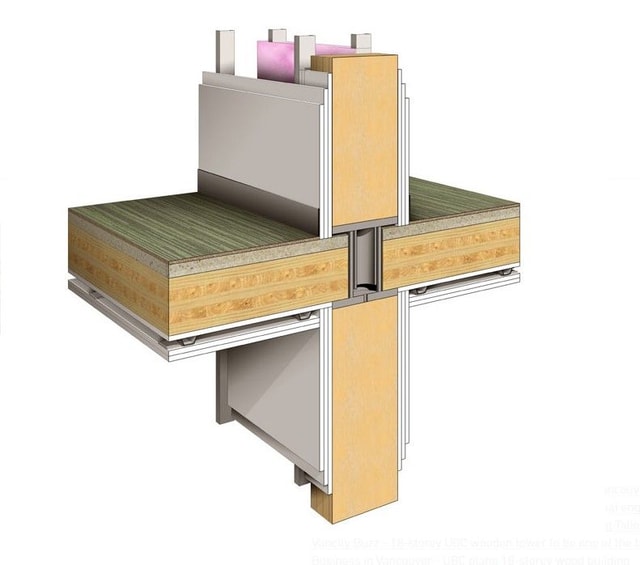
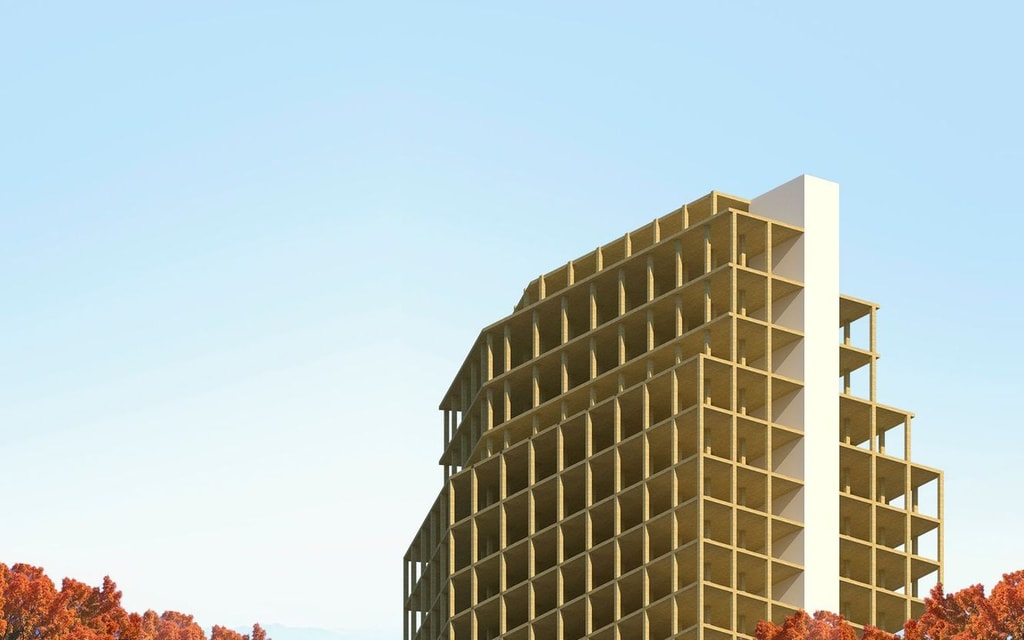
This momentum may be in response to the opportunities afforded by the new code provisions; nonetheless, there are numerous other noteworthy advantages to selecting mass timber that merit careful consideration. These include accelerated construction schedules, lighter timber superstructures, lower carbon footprints, minimisation of disruption to nearby communities and attractive, exposed timber finishes.
As an integral part of BDP Quadrangle’s Zero-Carbon Roadmap, we have initiated Whole Building Life Cycle Assessments (WBLCA’s) to understand the environmental impact of new projects. The broader goal of these assessments is to establish a comprehensive inventory of Life Cycle Assessment (LCA) data spanning multiple projects, enabling us to evaluate diverse methods and materials and to Make Embodied Carbon Part of the Decision-Making Process.
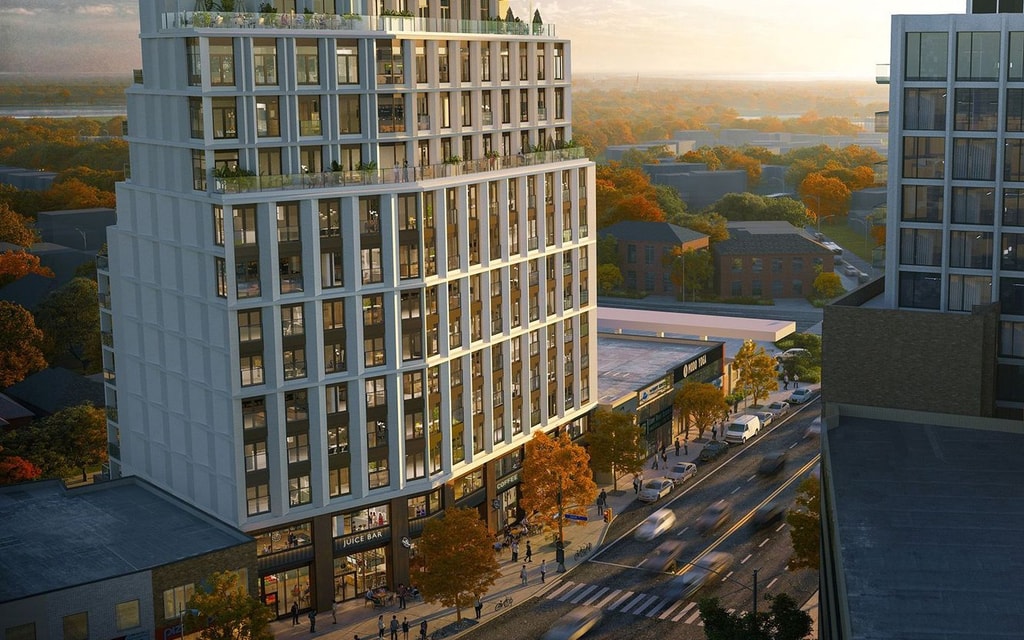
To illustrate this point, we conducted a preliminary LCA to quantify the embodied carbon impact of our project at 2453-2469 Bloor Street West, a mass timber midrise residential building recently submitted for preliminary municipal review.
Bloor Street West is conceived, designed, and constructed to protect and enhance the local community and its ecosystems. Opting for a mass timber structure, the floorplans are designed to offer plenty of outdoor space through balconies and terraces, using prefabricated timber for on-site assembly. As a result, the project achieved approximately 232 kgCO2e/m2 of embodied carbon, falling well below the voluntary targets introduced in Version 4 of the Toronto Green Standards.
As the demand for increased density near transit nodes and within existing neighbourhood zones intensifies, we see mass timber midrise development as a significant opportunity to address both the housing crisis and the need to adopt lower carbon construction methods. We continue to research the use of this material and discuss the future possibilities with our committed, climate conscious, multidisciplinary teams but to seize this opportunity, we aim to forge industry partnerships grounded in a shared commitment to improving the way we build on every new project.
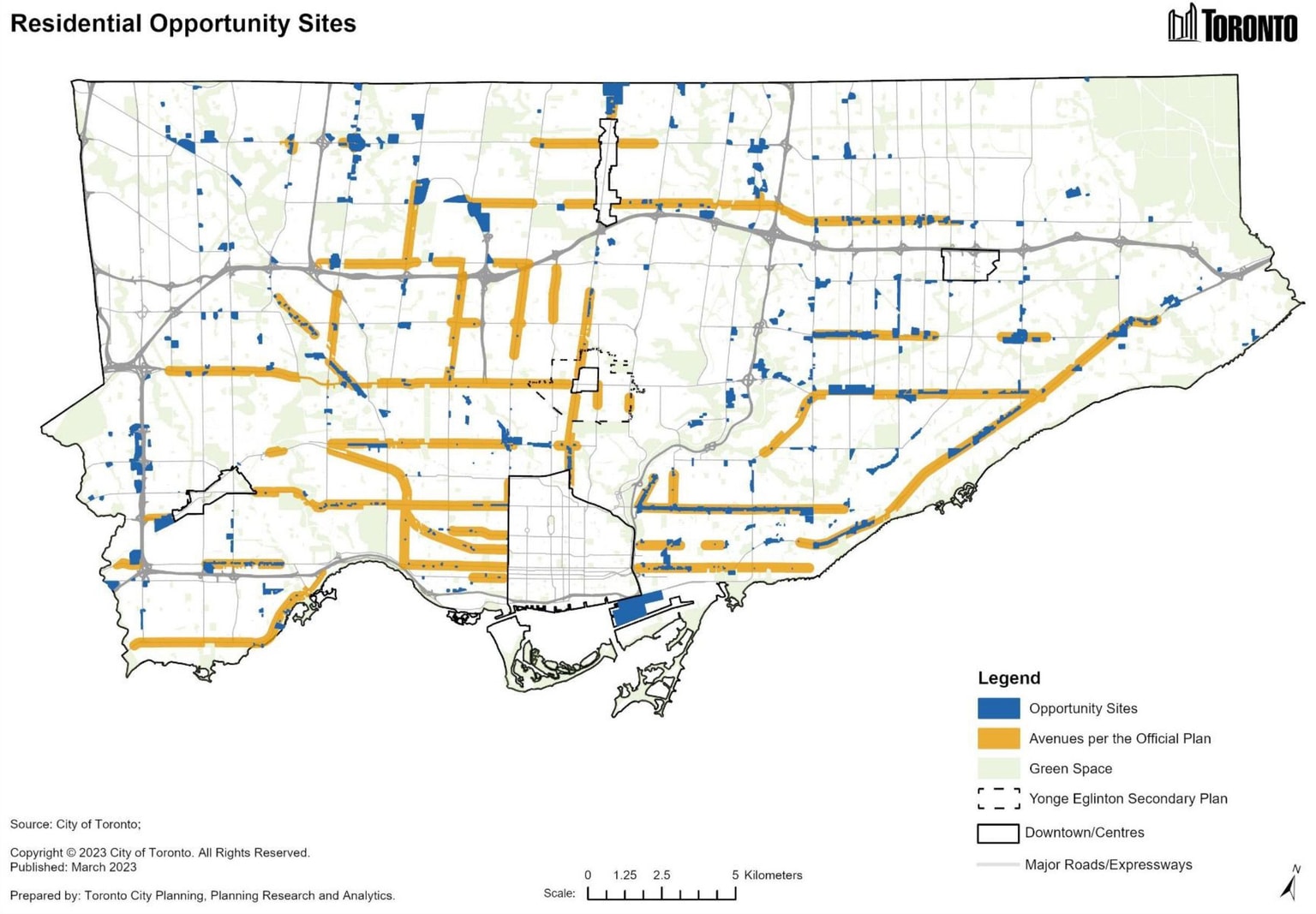
Related Links
2453 - 2469 Bloor Street West
A 12-storey mass timber residential building located on Bloor Street West at Jane Street in Toronto.
The urban umbrella
Adrian Price describes The Well, a vibrant new community in the heart of Toronto, designed to connect people with the city.